炭素繊維強化プラスチックの成型法
炭素繊維強化プラスチックの成型法について紹介します。
炭素繊維強化プラスチックには様々な成型法があり、作るものの大きさや必要な強度によって適切な成型法が変わります。
加えて、量産性が良い成型法もあればほとんど手作業で行われるような成型法もあり、作るものに対して適切な成型法を選択することが重要となります。
オートクレーブ法って何?
オートクレーブ法はCFRPの製法としては広く知られており、多種多様な部品の製造に使用される方法です。
オートクレーブ法で用いられる中間基材は、プリプレグです。
※プリプレグとは樹脂があらかじめ予備含侵された炭素繊維シートのことを指します。
公式JAXAチャンネルで紹介されているオートクレーブ法の動画を見てみてください。
オートクレーブ法
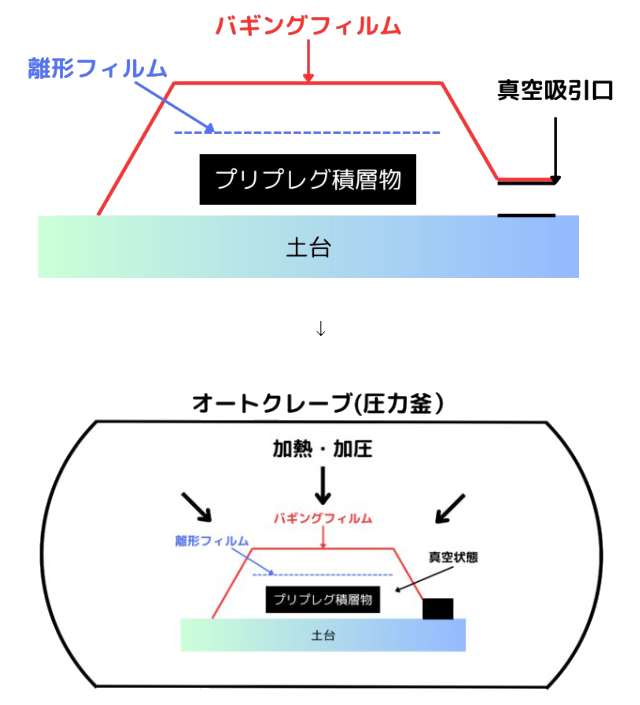
オートクレーブ法のメリット
- 真空状態で焼成するため、ボイドが形成されにくく高品質な成型物が得られる
- オートクレーブ内で全体(360°)から加圧されるため、高品質な成型物が得られる
- 複雑な形状を成型できる(板状・円筒形状共に)
- オートクレーブに入るサイズであれば、大きなサイズでも成型可能
オートクレーブ法のデメリット
- 多額の設備投資が必要
- 成型に手間がかかるので、成形コストが高い
- 手作業が多く、大量生産には向かない
シートワインディング法って何?
シートワインディング法に使用される中間基材は、プリプレグです。
”シート”はプリプレグのことを指します。
シートワインディング法
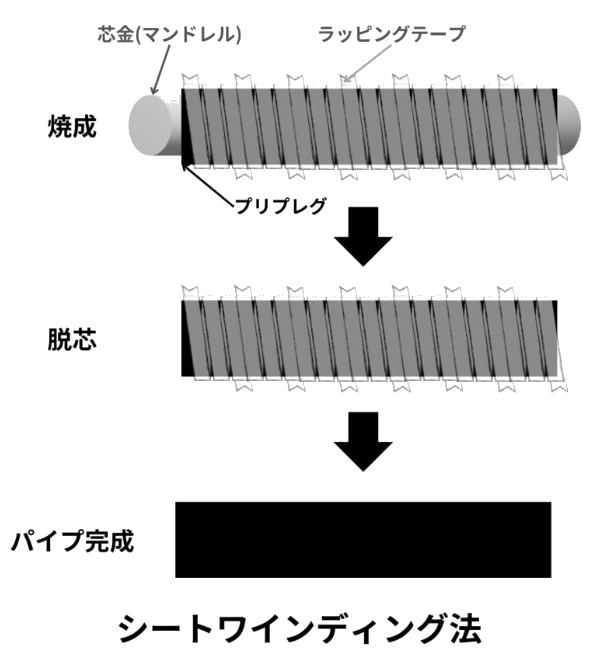
シートワインディング法のメリット
- 工程が比較的に簡単なので、量産性が良い
- 芯金を利用するため、内径の寸法精度が良い
- 円筒形状が作成可能
- 様々な繊維方向を組み合わせることが可能
シートワインディング法のデメリット
- 芯金の抜きテーパが必要なので、異形状の作成が不可
- 後加工なしだと外径が安定しない
- 円筒形状しか作成できない
プレス成型って何?
プレス成型に用いられる成型法は、プリプレグとSMC(シートモールディングコンパウンド)です。
プレス成型
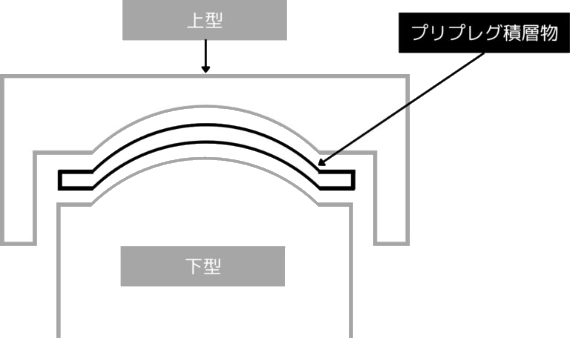
プレス成型のメリット
- 金型を温めたまま生産できるため、高サイクルタイム
- 全ての面が金型で成型されるため、寸法精度が良い
- 板形状が作りやすい
プレス成型のデメリット
- プレス機が必要
- 金型の抜きテーパを考慮する必要がある
- 真空状態での成型ではないので、層間や表面にボイドが形成される可能性がある
プレス成型の最大のメリットは、量産性です。
成型サイズは、大サイズの金型をプレス可能な設備があればかなり大きなサイズまで成型可能です。
全面金型での成型となるため寸法精度は良いですが、一方で抜きテーパを考慮すると成型可能な形状に制限があります。
内圧成型って何?
内圧成型で使用される中間基材はプリプレグです。
内圧成型で作られる代表例は、自転車のカーボンホイールです。
内圧成型
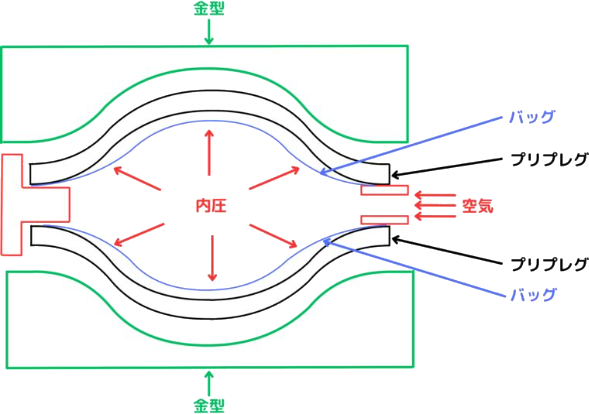
内圧成型のメリット
- 複雑形状の作成が可能
- 円筒形状の作成が可能
内圧成型のデメリット
- 内側には金型がないので、内径側の寸法精度が低い
- 複雑な形状になると、賦形に時間がかかる
内圧成型は内側からの空気圧で成型する方法であるため、他の成型法ではアンダー形状となるような形状でも作成可能です。
必然的に作成するものの形状が複雑になることが多く、賦形(レイアップ)に時間を要することなどから成形コストは高くなります。
また、内圧を受ける面には金型がないため、寸法精度が悪くなることも弱点です。
フィラメントワインディングって何?
フィラメントワインディング法は中間基材を用いず、炭素繊維そのものを使用する成型法です。
フィラメントワインディング法
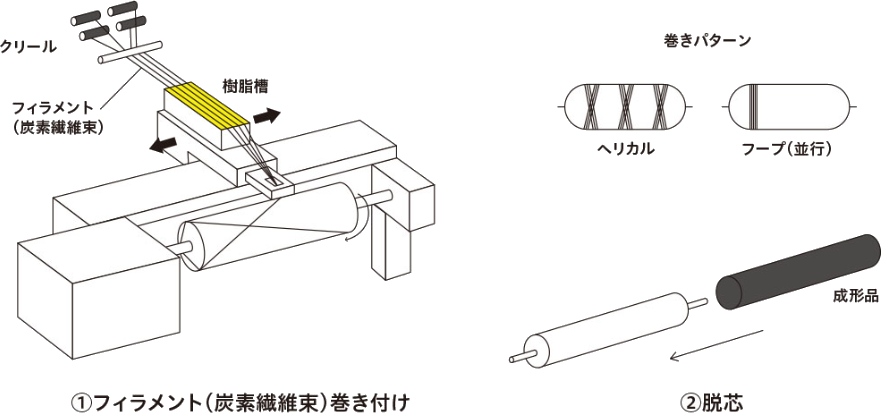
※東レカーボンマジック株式会社の図を引用
フィラメントワインディング法のメリット
- 自動化された成型方法のため、量産性が良い
- 品質が安定する
- 高い力学的特性
内圧成型のデメリット
- 多額の設備投資が必要
- 形状の自由度が低い
成形の方法としては芯金(マンドレル)を使用することなど、シートワインディング法と似ている部分があります。
この成型法の欠点は、シートワインディング法と同じく円筒形状しか成型できない事です。
一方で、長所は賦形の工程が自動化されていることであり、量産性が良いことや品質が安定することです。
炭素繊維強化プラスチックの成型法の中では自動化されていることは珍しいため、大きな長所と言えます!
レジントランスファーモールディング(RTM)って何?
レジントランスファーモールディング(RTM)法は、織物(クロス)などのドライ中間基材を用いる成型法です。
レジントランスファーモールディング(RTM)法
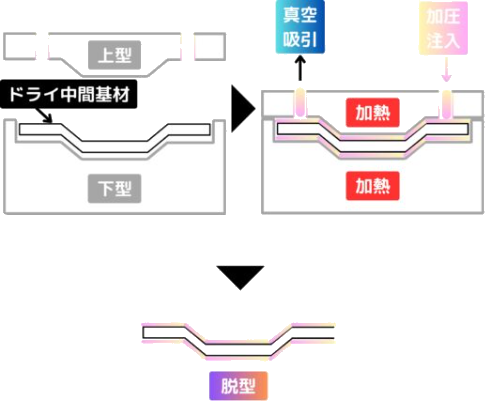
RTM法のメリット
- 高サイクルタイムによって、量産性が良い
- 品質が高品質で安定する
- 複雑形状の成型が可能
RTM法のデメリット
- 多額の設備投資が必要
- 金型の抜きテーパを考慮する必要がある
- 樹脂の流動性が悪いとボイドが発生する
- 高圧で樹脂を注入する際に、炭素繊維が蛇行する
先に紹介したプレス成型法と似ていますが、プレス成型法では樹脂含侵中間基材を使用するのに対して、RTM法ではドライ中間基材を使用する点が大きく違います。
この違いによって大きく変わる点は、成形可能な形状の自由度です。
プレス成型は金型の圧力のみで、樹脂含侵中間基材(プリプレグやSMC)に含まれる樹脂を流動させるため、板形状の成形がメインとなります。
一方で、RTM法では高圧で樹脂を注入し樹脂流動させるため、3次元的な形状も成型可能です。
プルトージョン(引き抜き)法って何?
プルトージョン(引き抜き)法は中間基材を用いず、炭素繊維そのものを使用する成型法です。
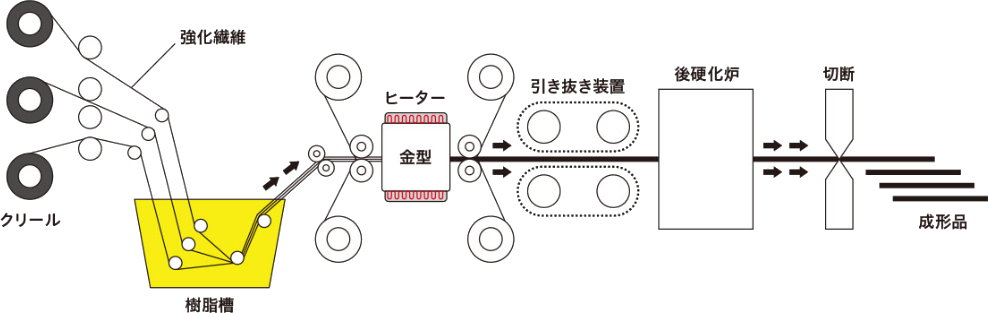
※東レカーボンマジック株式会社の図を引用
プルトージョン(引き抜き)法のメリット
- 連続的な成型が可能なため、量産性が良い
- 成型時の無駄な材料が少ない
- 品質が安定している
プルトージョン(引き抜き)法のデメリット
- 成型可能な形状に制限がある(断面形状が一定でなければならない)
- 多額の設備投資が必要
- 一方向にしか繊維を配置させることができない
射出成型(インジェクション)法って何?
ペレットは下記の写真のように、粒状の中間基材です。
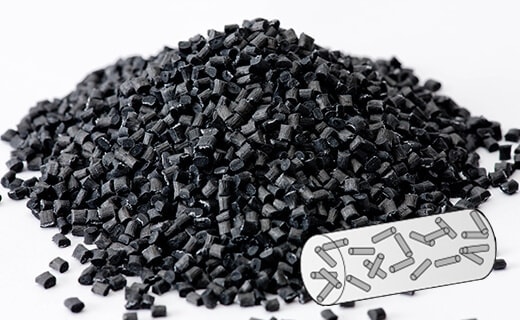
射出成型法
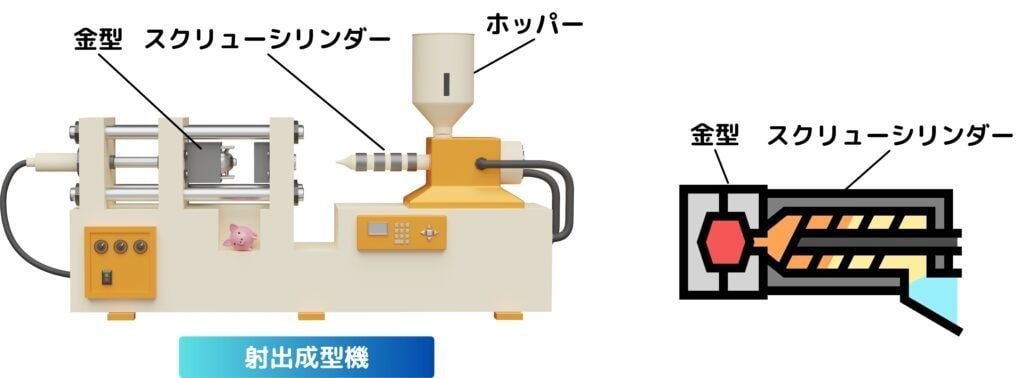
射出成型(インジェクション)法のメリット
- 高サイクルタイムで量産性が良い
- 自動化されているため品質が安定する
- 複雑形状の成型が可能
- 熱可塑性樹脂を使用するため、リサイクルが可能
プルトージョン(引き抜き)法のデメリット
- 力学的特性が低い
- 金型費が高い
- 寸法精度が低い(ひけ・そり)
射出成型によって作られる成型品は、炭素繊維が短くカットされている・繊維方向がランダムであるという二点から力学的特性が低いことがデメリットです。
一方で、サイクルタイムや量産性は本記事で紹介した成型法の中で随一と言っても良いでしょう。
従って、強度や剛性がそこまで必要なく大量生産する小型部品が射出成型に最も適しているといえます。